BENEFITS FOR YOU WORKING WITH RAISE3D AND FORWARD AM
Top-grade materials, steadfast reliability and applications across every industry.
FORWARD AM & RAISE3D CONTENT
An end-to-end fully integrated in-house printing Metal Ecosystem
October 28th, 2021. Rotterdam – Raise3D, the global provider of additive manufacturing solutions for SMEs and LSEs, announces the worldwide launch of Raise3D MetalFuse system, an end-to-end fully integrated in-house printing ecosystem for metal 3D printing, developed in close collaboration with Forward AM and using Ultrafuse® Metal Filaments.
Raise3D MetalFuse, a 3D Printing full in-house solution, using Ultrafuse® Metal Filaments
E2CF especially designed for printing with composite filaments
Engineering filaments, especially high-performance composite filaments give 3D printing professionals many competitive edges. E2CF is specially designed for composite filaments, wear resistance and moisture control are important by printing with composite filaments, reliability, repeatability and reproducibility are the keys to the high-performance printed part. Optimized and fine-tunned, and even customized printing profiles for OFP 2.0 filaments are favored by many industrial customers. All of these mentioned above, we can trust Raise3D E2CF. – Dean Di, R&D Engineer at Forward AM
This partnership allows customers to experience the benefits of top-grade materials, steadfast reliability, and the versatility to create parts for applications across every industry.
Whether you manufacture components for the automotive, education, or aerospace sector, you can be sure that your Raise3D hardware, in combination with our BASF Forward AM Ultrafuse® filaments, will adhere to your every need.
Is this the first time with this machine material combination? At our valuable resources, you will find everything you need.
INTRODUCING RAISE3D METALFUSE
Raise3D MetalFuse, a 3D Printing full
in-house solution, using Ultrafuse® Metal Filaments
“The collaboration with Forward AM is a milestone in Raise3D’s history, and a solid step towards our vision of offering a perfect ecosystem to facilitate Flexible Manufacturing. Our Raise3D MetalFuse system combined with Ultrafuse® Metal Filaments from BASF Forward AM offers a solution to additive manufacturing of metal parts that is easier, safer, cleaner, cheaper, and faster, than the current AM metal parts productions, making it accessible to everyone using those solutions. In many cases, we have also confirmed that Raise3D MetalFuse can be competitive with MIM, which makes us confident that MetalFuse can represent a breakthrough in metal parts production”
Validated Raise3D Printers
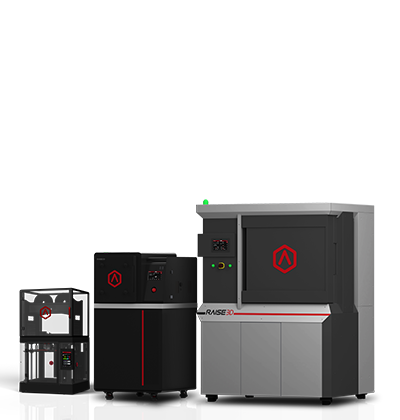
Metal Fuse - Ecosystem
A 3D Printing Full in-house solution which allows small batch production of metal parts.
Read more
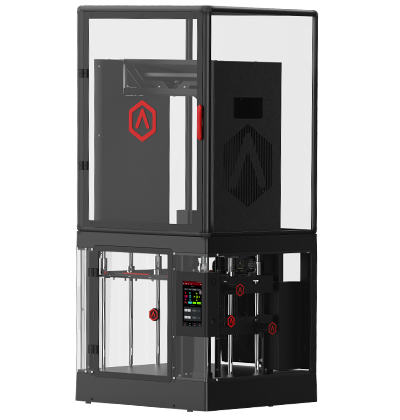
Raise3D Forge 1 Metal Fuse
MetalFuse offers a complete solution, consisting of an indirect metal 3D printing process, paired with a special edition of ideaMaker compatible with MIM equipment
Compatible filaments
Compatible with the following Ultrafuse® materials;
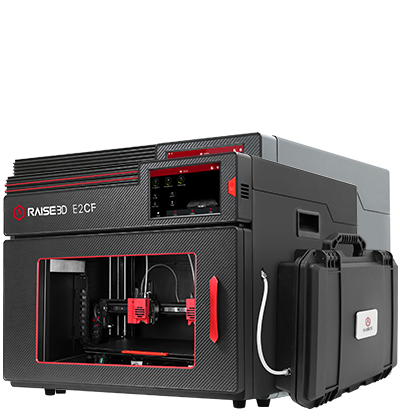
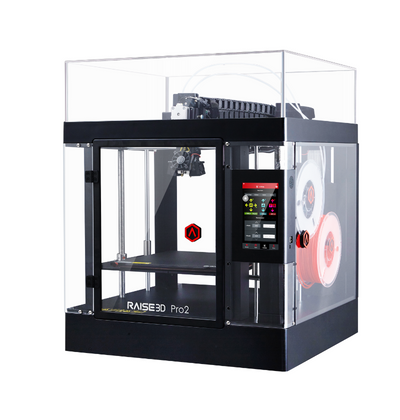
Raise3D Pro2 Series
The Pro2 Series has a metal build plate for even heat distribution, along with a full metal frame for smooth movement and precise positioning, and is compatible with a variety of 3D printing materials.
Compatible filaments
Compatible with the following Ultrafuse® materials;
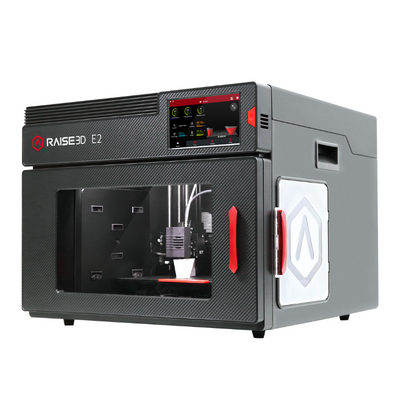
MATERIAL PRINTER COMPATIBILITY TABLE
Raise3D Metal Fuse with Ultrafuse® Metal Filaments
A 3D Printing Full in-house solution, using our Ultrafuse® Metal Filaments and Raise3D hardware, which allows small batch production of metal parts, with full design freedom and a low cost of ownership
Raise3D MetalFuse system comprises the desktop metal 3D printer Forge1, the catalytic debinding furnace D200-E, the sintering furnace S200-C, the slicer ideaMaker Metal, and uses Ultrafuse® Metal Filaments from BASF Forward AM.
Read more about Metal Fuse
Raise3D MetalFuse is the first complete in-house solution optimized for Ultrafuse® Metal Filaments
Besides the benefits resulting from the great properties of these filaments, being a complete in-house solution has the additional advantages of:
• Speed, by avoiding the need to interact with third parties, substantial time can be saved, making it possible to go from the initial “idea” to the “final part” in a couple of days;
• Minimizing the handling of the ‘green parts’;
• Ensuring full confidentiality, by having the full process in-house, as opposed to when the debinding and sintering need to be done externally.
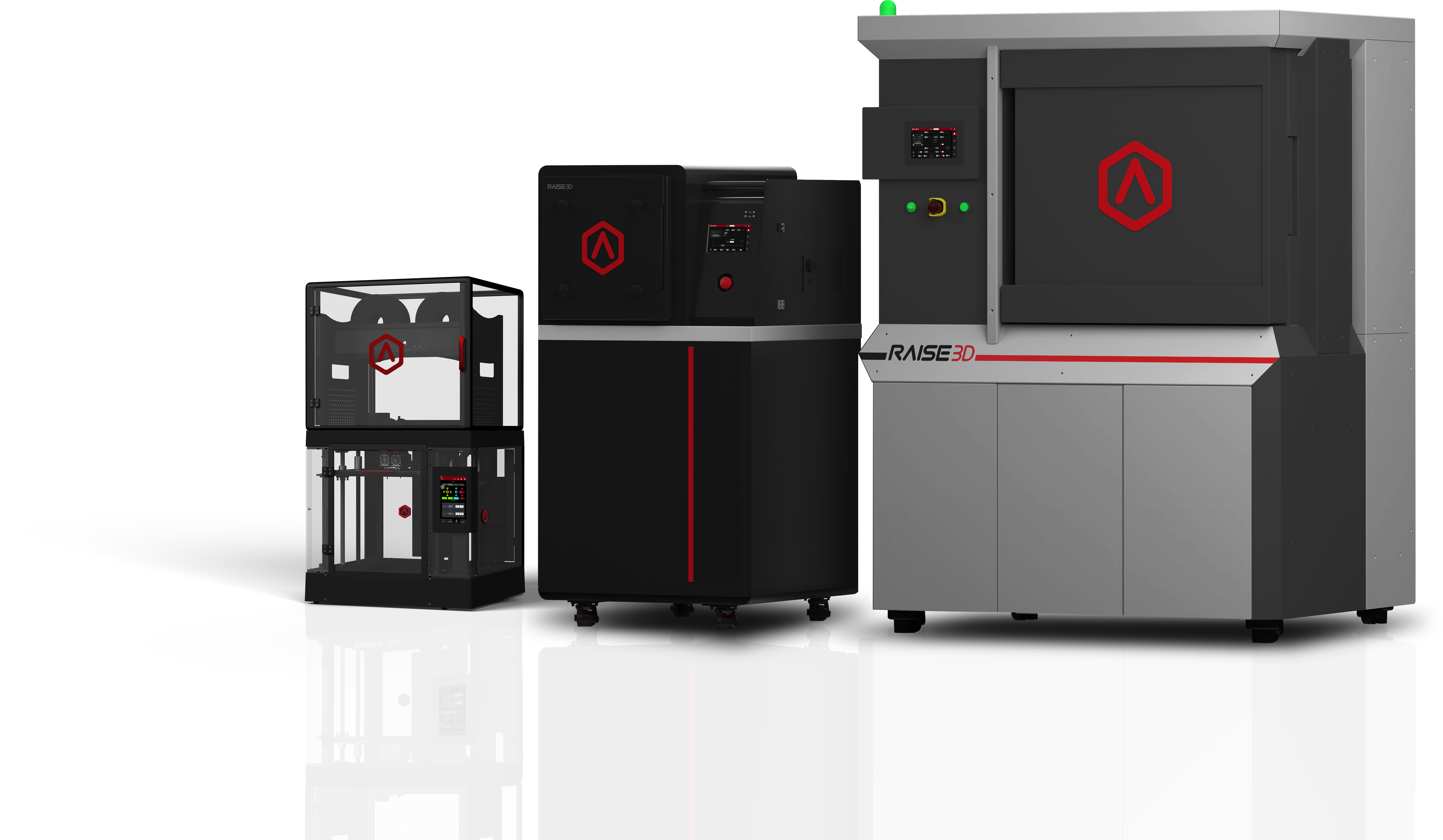
“Metal FFF offers great advantage to the customers; it is affordable, easy to use and eliminates a very complex step in comparison to other Metal AM techniques like powder handling. According to Hizal, “MIM technology can be the best solution to manufacture parts in large volumes, whereas Metal FFF can be used to produce more sophisticated designs in small and medium size batches. We are very impressed by the capabilities of MetalFuse ecosystem and convinced that Raise3D MetalFuse together with our Ultrafuse® Metal Filaments, will deliver excellent value to customers. We are installing our first Raise3D MetalFuse unit in our facilities in Shanghai soon. We will continue working closely with Raise3D to further optimize the MetalFuse ecosystem”.